Spring 2023-Present
Ornithopter
Designing a Flapping Wing Unmanned Aerial Vehicle

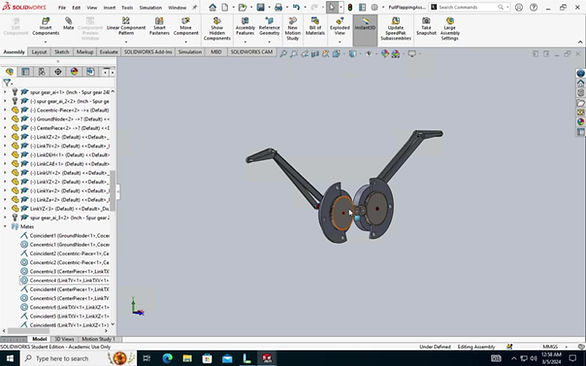
Background
My research aims to design an unmanned aerial vehicle (UAV) capable of sustained and controlled flight using a flapping wing mechanism. My partner and I have defined 'successful' flight as lasting a minimum of one minute, distinguishing it from mere floating or gliding.
Traditionally, UAVs have been categorized into two primary types: fixed-wing and multirotor. However, both designs come with tradeoffs. Multirotor drones offer hovering capabilities and some maneuverability but suffer from shorter flight times and increased noise due to high rotor speeds. Conversely, fixed-wing drones boast longer flight times but lack hover capabilities, have limited maneuverability, and require high forward speeds to stay airborne.
Flapping-wing UAVs, also known as ornithopters, present a promising alternative. They offer superior aerodynamic performance, increased maneuverability, and the ability to hover when needed. When birds flap their wings, they passively generate lift due to the flexible nature of their wings interacting with the air's aerodynamics. In contrast, multirotor drones rely solely on active propulsion, leading to higher energy consumption. Similarly, traditional airplanes rely on engines for thrust, using wings primarily for lift. However, flying animals use their wings for both thrust and lift, resulting in lower energy consumption and the ability to exploit air currents.
By emulating the flight mechanics of birds, ornithopters can operate at lower speeds, enhancing maneuverability and enabling hover capabilities.
Spring 2023
Given the complexity of the engineering challenge, we divided the project into three segments. The first semester was dedicated to conducting background research on existing ornithopters and determining the airfoil type and size scale for our vehicle.
During this phase, we delved into the study of morphing airfoils, which presented an exciting opportunity to enhance our design's energy efficiency. Inspired by the structure of a fish skeleton, we explored various models—both physical prototypes and digital simulations in Solidworks—to examine the impact of thickness and layer count on the airfoil's performance.
Following assembly, we utilized Solidworks Computational Fluid Dynamics (CFD) to analyze how alterations in the airfoil's shape influenced lift and drag forces. Additionally, we ensured that our designs distributed stress flows uniformly throughout the material, avoiding potential stress concentration areas.


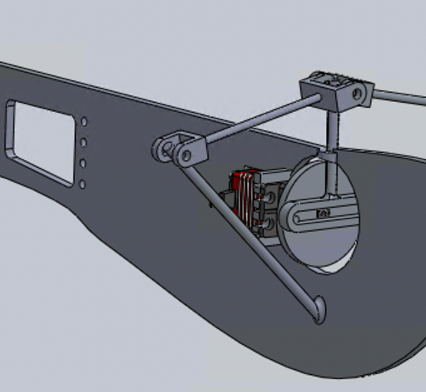
Fall 2023
We simplified the problem by reducing the flapping amplitude to 0º, essentially creating a fixed-wing configuration. This adjustment allowed us to focus on ensuring the bird's weight distribution would support sustained flight once we incorporated the more intricate scotch yoke flapping mechanism. To prevent stalling, it's crucial for the vehicle's center of gravity to be slightly forward of the quarter chord.
​
Naturally, there's a tradeoff between weight and power: more powerful motors tend to be heavier. In our prototype, I opted for the HSB-9360TH high-speed motor, which is heavy but offers exceptional power. While the current prototype has not undergone comprehensive testing, we plan to conduct thorough tests at the beginning of the next semester.
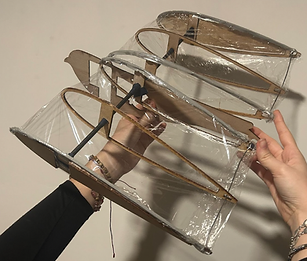
Spring 2024... Stay tuned!
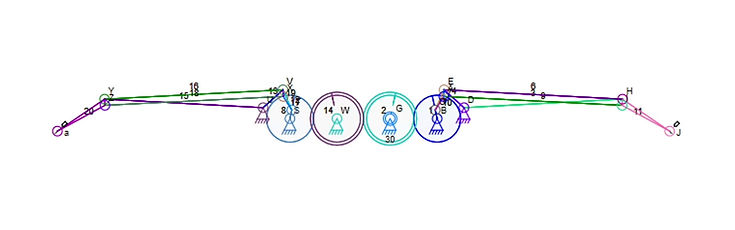